We receive materials of any kind in the pre-treatment station, such as for example typical sweepings, borax, crucibles, sludges of goldsmiths’ and silversmiths’ companies, as well as spent catalysts that are thermally treated or milled, or any material which has previously been calcined in the customer’s facilities, that has to be recovered. Metallic waste (mainly from silverware and gold items) is smelted and sampled in a dedicated line, which is located in an armored facility due to the high concentration of precious metals, and it is shipped to undergo recovery through refining.
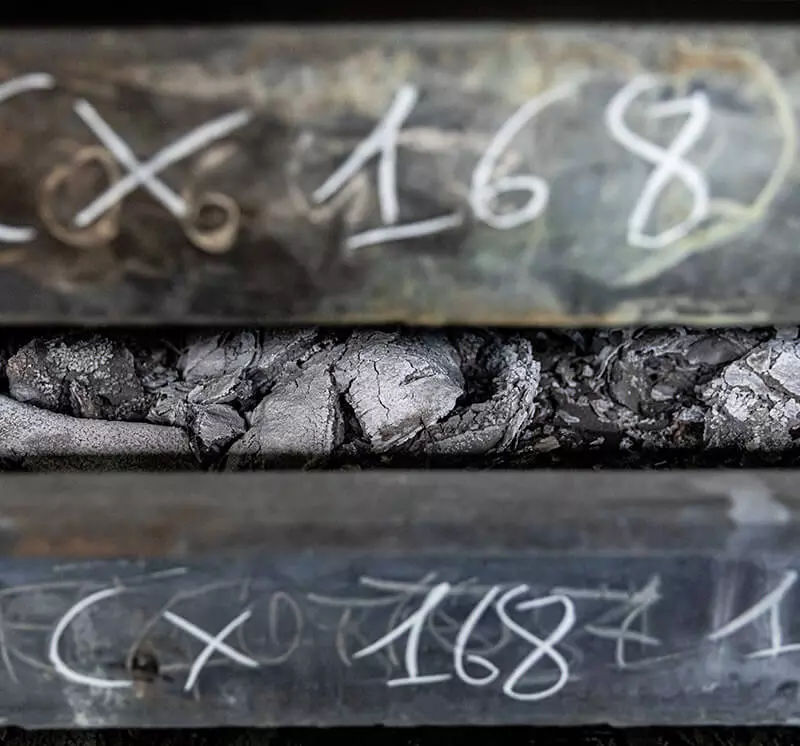
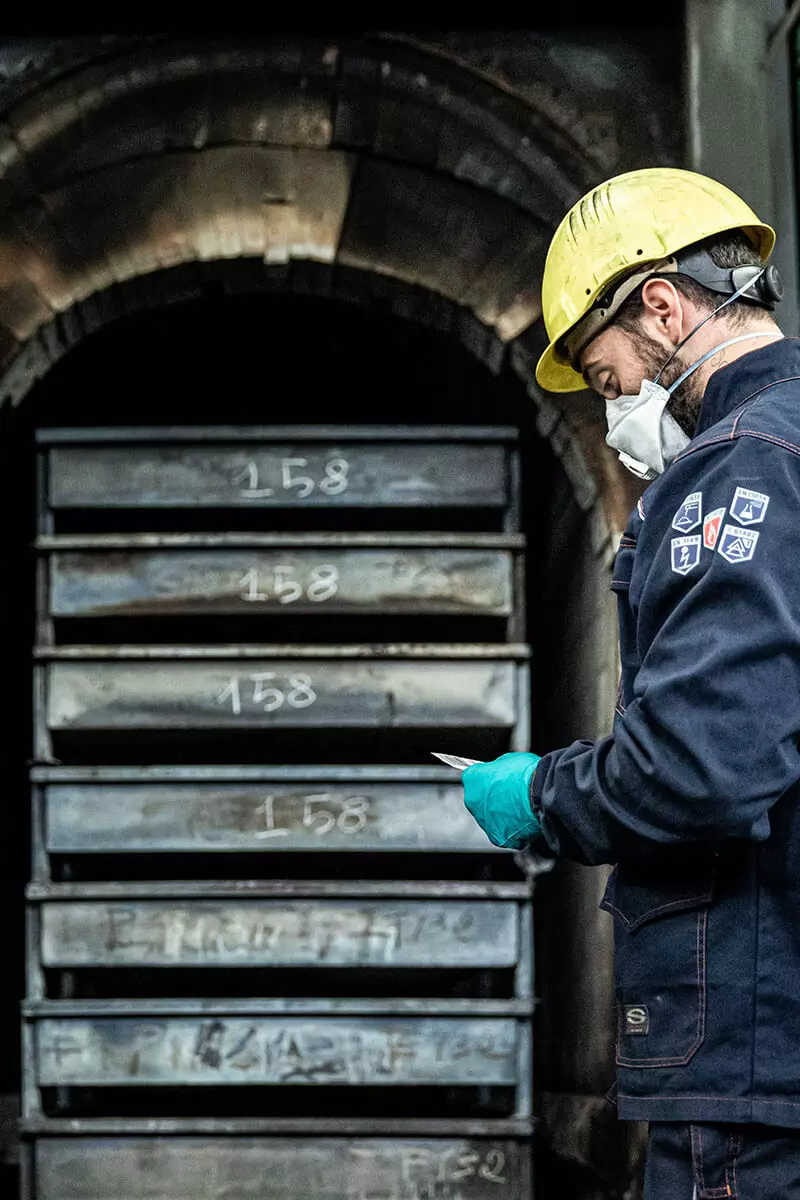